Bringing workforce management and quality management together to engage employees and boost CX
- 1. Introduction
- 2. Key Takeaways
- 3. Exploring the Essentials of Quality Management Systems (QMS)
- 4. The Pillars of Total Quality Management (TQM)
- 5. Driving Forces Behind Quality Planning and Control
- 6. Quality Assurance: Building Confidence in Your Brand
- 7. Optimizing Business Processes for Quality Outcomes
- 8. Leveraging Enterprise Quality Management Software (EQMS)
- 9. Quality Management in Action: Case Studies and Success Stories
- 10. Quality Management Insights: Expert Opinions and Future Trends
- 11. Summary
- 12. Call to Action
- 13. Frequently Asked Questions
Key Takeaways
- Quality Management Systems (QMS) are foundational frameworks for enterprises to deliver consistent quality in products and services, involving meticulous planning, stakeholder engagement, and data-driven decision-making to meet customer and regulatory demands.
- Total Quality Management (TQM) is a strategic, customer-focused approach that incorporates continuous improvement and total employee commitment into the fabric of an organization’s processes, with leadership playing a key role in championing customer satisfaction initiatives.
- Enterprise Quality Management Software (EQMS) centralizes and standardizes quality management data, offering features like real-time data monitoring and scalability to improve business performance and adapt to growth.
Exploring the Essentials of Quality Management Systems (QMS)
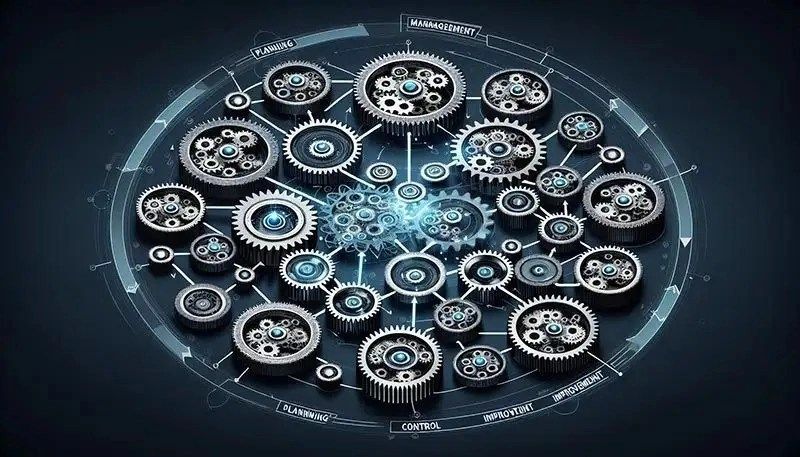
Defining Quality Management System (QMS)
A Quality Management System (QMS) is a structured collection of business processes, focused on consistently meeting customer requirements and enhancing their satisfaction. It’s a documented and formalized process that defines the steps, expected outcomes, improvements, and results, ensuring that a company’s offerings align with customer and regulatory demands. While many may equate a QMS with the ISO 9001 standard, it’s essential to understand that a QMS encompasses the entire system an organization employs to manage quality, including all necessary documentation.ISO 9001:2015 is merely one framework that provides specific requirements for a quality management system.The Importance of QMS in Meeting Customer Satisfaction
Customer satisfaction sits at the heart of a Quality Management System. By understanding and aligning with customer needs and expectations, companies ensure that their products and services consistently hit the mark. The key to customer retention and attraction is the ability of a QMS to produce reliable and high-quality outcomes, which in turn fosters customer loyalty.Take companies like HFI or Vishay Dale Inc., for instance, which have demonstrated how an effective QMS can streamline operations and spur growth, showing the symbiotic relationship between customer satisfaction and quality management.Key Elements of an Effective Quality Management System
An effective QMS is not a one-size-fits-all solution; it is tailored to the unique needs of an organization. It typically involves a blend of overarching quality philosophy, quality assurance, and quality control. A strategic approach to quality management helps develop a culture that prioritizes product quality, profitability, and employee engagement.Moreover, an evolving QMS is one that is deeply interconnected with customer experiences, drawing on feedback to elevate products and services. At the crux of quality management is data-driven decision-making, which relies heavily on data analysis and systematic information gathering to make informed choices, understand market trends, and grasp customer needs.The Pillars of Total Quality Management (TQM)
Embracing Continuous Improvement
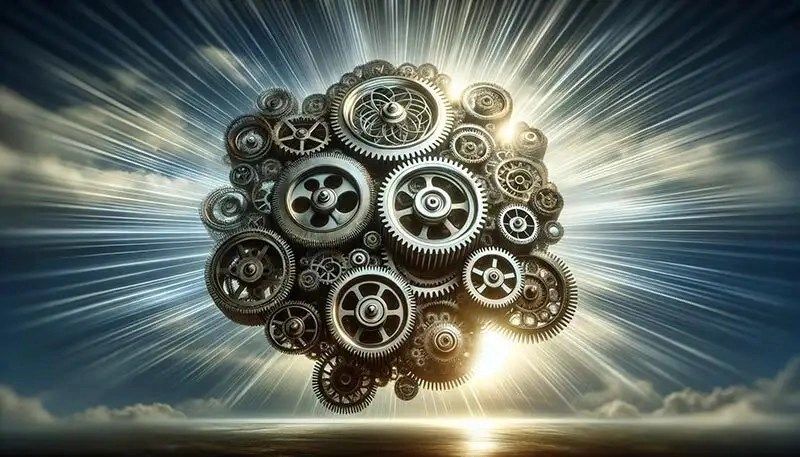
Achieving Customer Focus
A customer-focused approach is paramount in TQM and involves every team member from top leadership to front-line staff. Leaders particularly play a pivotal role in championing customer satisfaction initiatives, ensuring customer service remains a strategic priority, and allocating the necessary resources.By incorporating customer feedback mechanisms into business processes, organizations can rapidly adapt to customer needs and refine their offerings accordingly. Some ways to do this include:- Conducting customer surveys
- Monitoring social media for customer feedback
- Implementing a customer feedback hotline or email address
- Holding focus groups or customer advisory boards
Integrating TQM into Organizational Processes
For TQM to be effective, it must be woven into the very fabric of an organization’s processes. This means fostering a quality-focused work culture where every employee understands and contributes to the quality objectives. Data plays a critical role in TQM, with objective data analysis leading to better quality management decisions and increased confidence in those processes.Beyond merely assuring quality, TQM requires a proactive stance in identifying and resolving quality issues as they emerge, ensuring a seamless integration of quality across the business.Driving Forces Behind Quality Planning and Control
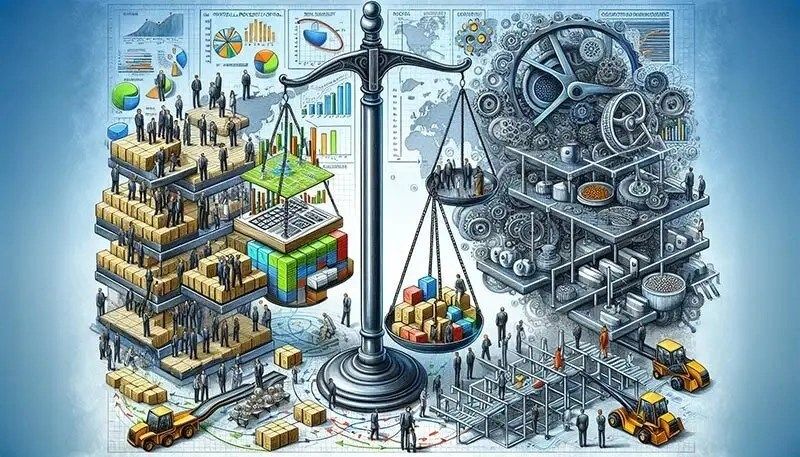
The Role of Statistical Process Control in QMS
Statistical Process Control (SPC) plays a pivotal role within QMS, monitoring and controlling production processes to ensure that quality standards are met with consistency. SPC employs a suite of quality control tools, including cause-and-effect diagrams and control charts, helping shift the focus from defect detection to prevention. This proactive approach not only enhances process performance but also lowers the risk of potential negative impacts.In essence, SPC underpins risk management within quality planning, identifying potential quality issues early on and facilitating proactive measures to mitigate risks.Risk Management as a Quality Planning Tool
Risk management is an integral part of quality planning, equipping organizations to anticipate potential quality challenges before they become problematic. Identifying potential issues ahead of time allows for the creation of specific actions and contingency plans to address anticipated challenges, ensuring maintenance of quality standards despite unforeseen disruptions.Quality Assurance: Building Confidence in Your Brand
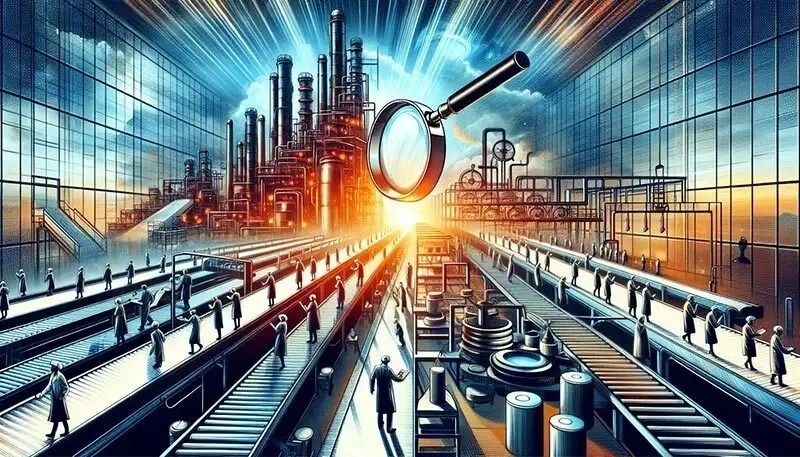
Maintaining Regulatory Compliance
Regulatory compliance is a critical aspect of quality assurance, particularly in industries governed by stringent regulations such as healthcare and pharmaceuticals. An EQMS can provide the necessary tools to ensure compliance, automating training management and streamlining adherence to data security and privacy regulations like ISO 27001 and GDPR.Choosing the right EQMS, therefore, requires an understanding of industry-specific compliance needs and the expertise provided by the software.The Impact of Quality Assurance on Customer Trust
Quality assurance significantly influences customer trust, which is foundational to strong customer relationships and brand loyalty. By adhering to quality assurance practices, organizations can ensure that they consistently meet and exceed customer expectations, thus strengthening consumer trust and giving them a competitive edge in the market.Optimizing Business Processes for Quality Outcomes
The optimization of business processes is essential for achieving quality outcomes. The process approach ensures:- Efficiency and effectiveness in organizational operations
- Improved consistency
- Reduced costs
- Waste elimination
Streamlining Supply Chain Operations
Streamlining supply chain operations is crucial for maintaining quality throughout the product lifecycle. Automation of tasks addresses bottlenecks and enhances efficiency, while investment in process automation software can lead to significant time and cost savings.By incorporating stringent quality standards and standardizing processes, businesses can ensure smoother operations and more reliable service delivery.Enhancing Production Schedules for Timely Delivery
Effective production scheduling is vital for ensuring timely delivery of products. To achieve this, you need to:- Understand production capacity and accurately calculate lead times.
- Use demand forecasting to anticipate customer needs and plan production accordingly.
- Balance machine and labor availability to avoid bottlenecks and minimize downtime or overtime costs. By following these steps, you can achieve a smoother production process and ensure on-time deliveries.